System Features

The design technology of turbine expander is more mature.

Distributed design, single machine can achieve small power to high power arbitrary design.

Unit cost is low, and the cost of single high-power machine is relatively low compared with that of many parallel small units.
Coal chemical enterprise gasification unit low flash steam waste heat power generation project
|
According to the site situation, the content of technical reform is:
A new 2.2MW split ORC turbine expansion power generation system was added
|
Project Process Drawing
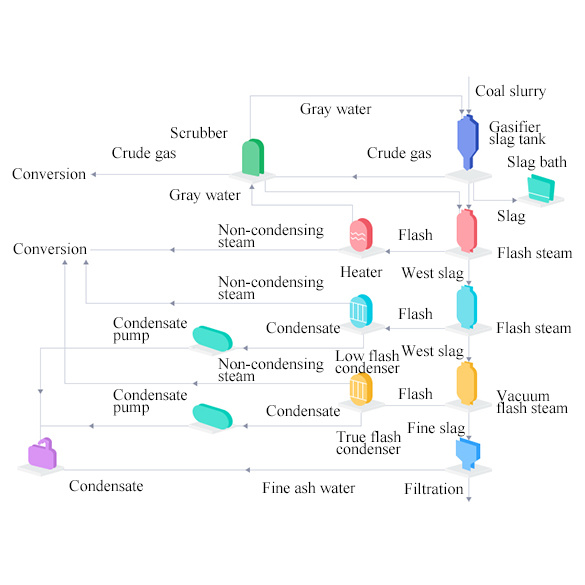
Heat source process flow chart
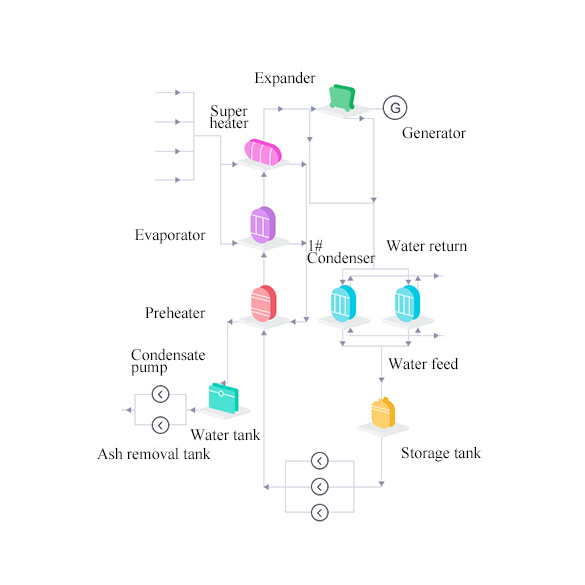
Waste heat power generation PFD
Retrofit Scheme
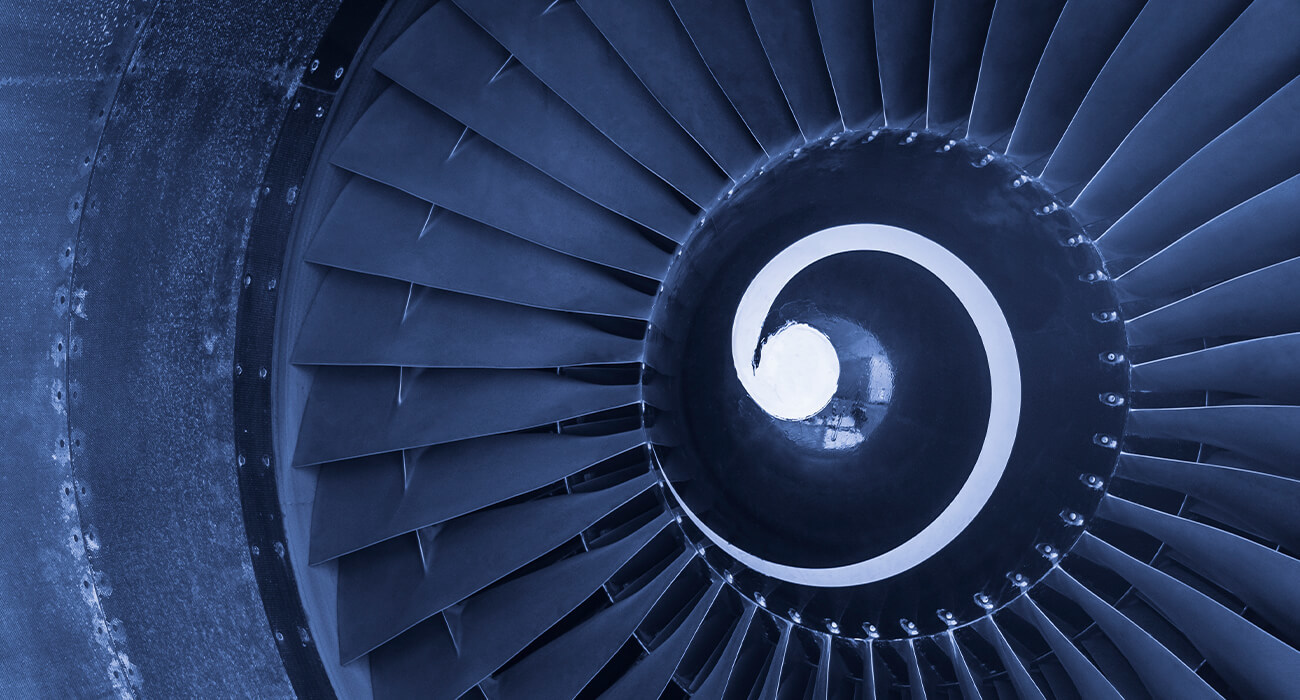
Host Selection Introduction
This series of products adopts stable and mature axial flow ORC turbine + generator from Boomtec and adopts mechanical dynamic seal, which can basically achieve zero leakage requirements. (ORC unit has 7 years of stable operation performance, was listed by the national Ministry of Industry and Information Technology as a key energy-saving demonstration project in 2018) turbine adopts radial intake, axial exhaust, double support structure, impeller form is multi-stage axial flow, by the intake chamber, stator ring assembly, housing, exhaust vortex housing, bearing, rotor of turning motor and other components. The working medium is R245fa (pentafluoropropane).
The seal is double-end mechanical seal to ensure that the working medium does not leak to the maximum extent. The sealing fluid system adopts PLAN54 independent sealing fluid system according to API682 standard to ensure that the sealing fluid oil cooling and lubrication of the sealing friction surface, while ensuring that the sealing fluid oil pressure is about 0.2MPa higher than the organic working medium pressure to prevent the leakage of the working medium. Blade profile selected for R245fa special blade profile, multi-stage axial flow reaction type. Cast steel 25 casting molding, smooth flow path, beautiful appearance. The generator adopts positive pressure ventilation type asynchronous generator.
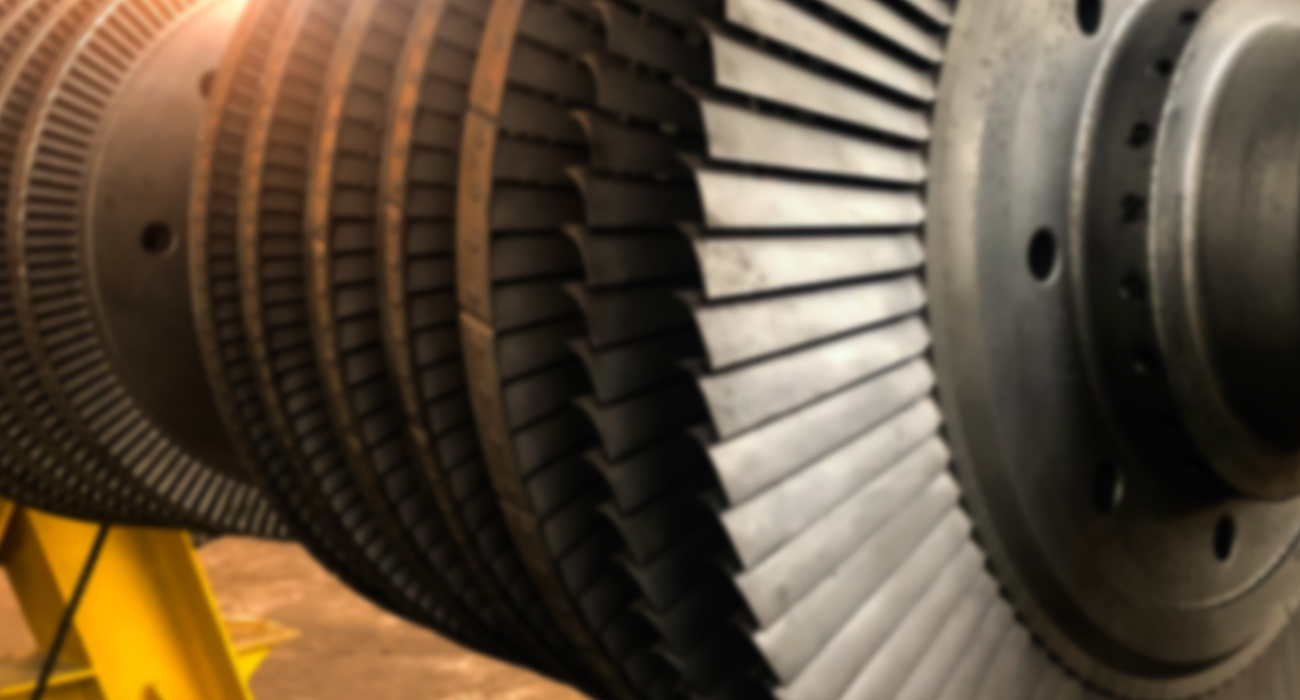
Evaporator, preheater design features
Shell-and-tube heat exchangers are used in the evaporator and preheater in this project. As the black water flash steam contains corrosive substances, 316L stainless steel is used in the evaporator and preheater to prevent corrosion in the parts in contact with the flash steam and its condensate. Black water flash steam contains a small amount of non-condensing steam, and the heat exchangers are equipped with vent valves to discharge non-condensing steam.
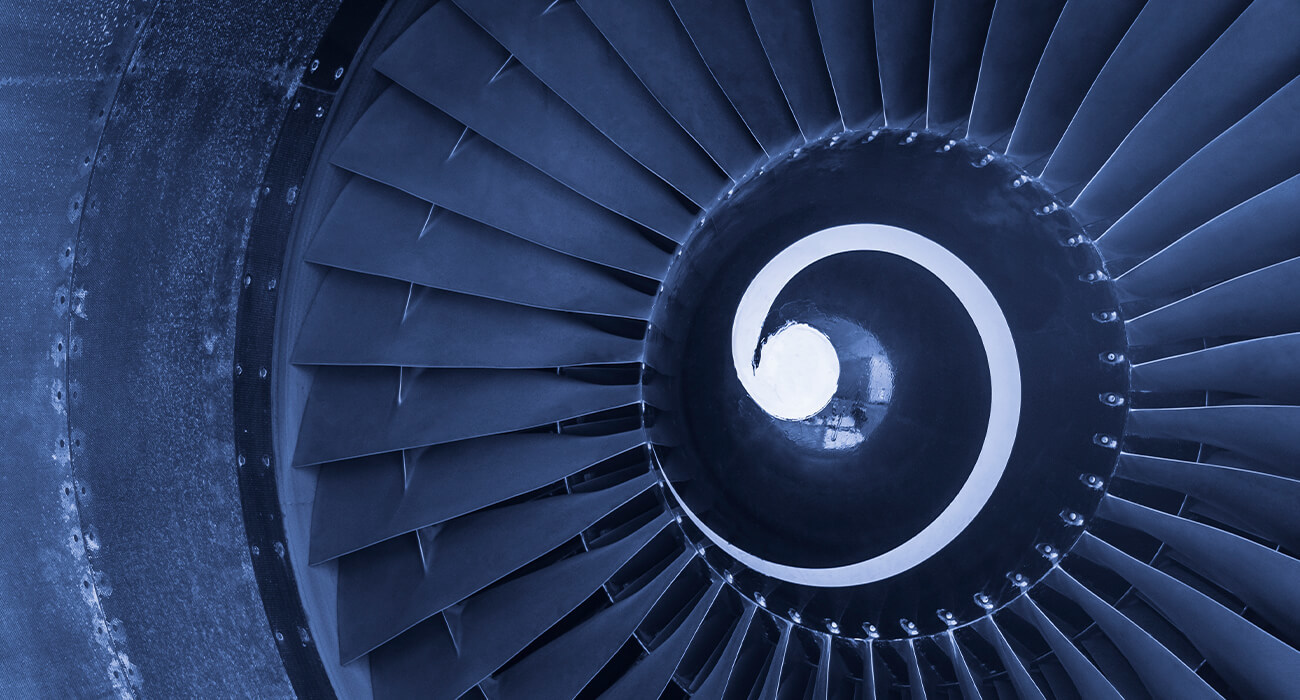
Condenser design features
Shell and tube heat exchangers are used in the condenser of this project, and the heat exchange tubes are treated by special technology. The organic working fluid vapor condenses through the shell side, and the coating can effectively prevent the corrosive ions in the circulating cooling water from corroding the heat exchange tubes.
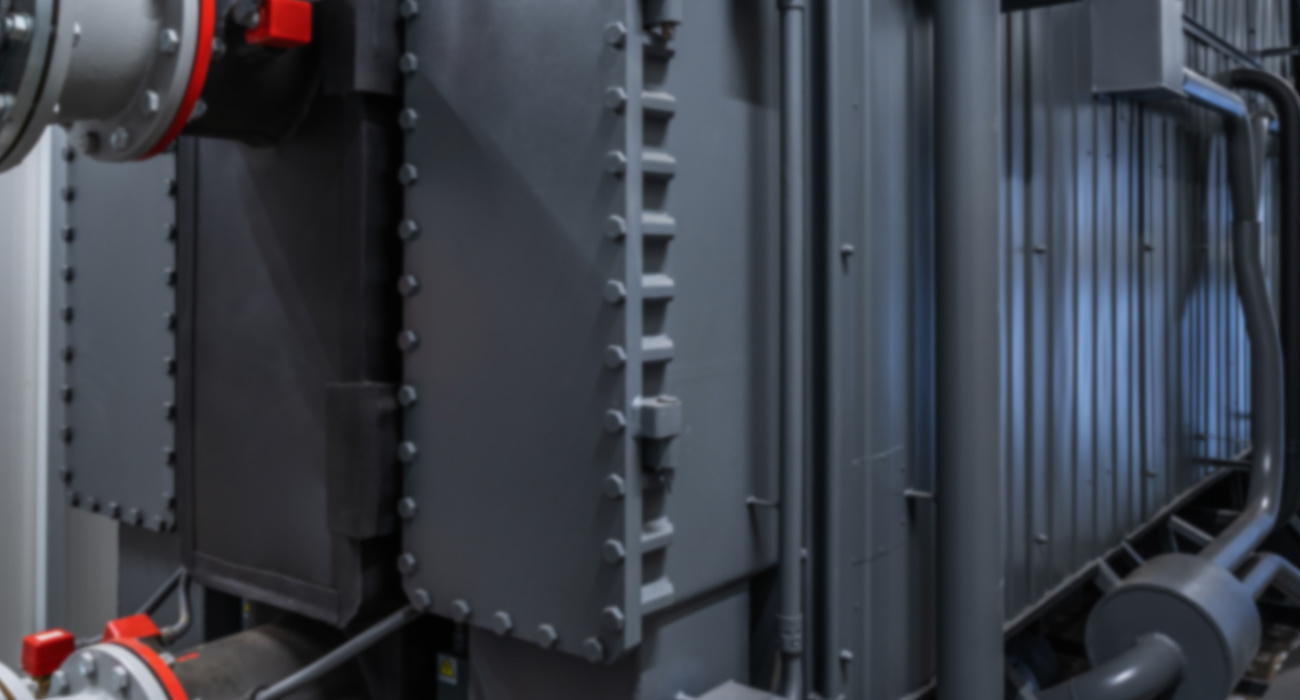
Working medium pump selection introduction
The working medium pump of this project adopts a shielded pump, which can prevent the leakage of organic working medium. The working medium pump adopts three pumps of the same model, which are used for dual use and one standby. When the working medium pump needs maintenance, it can be quickly switched to the standby pump to ensure the safe and stable operation of the system.
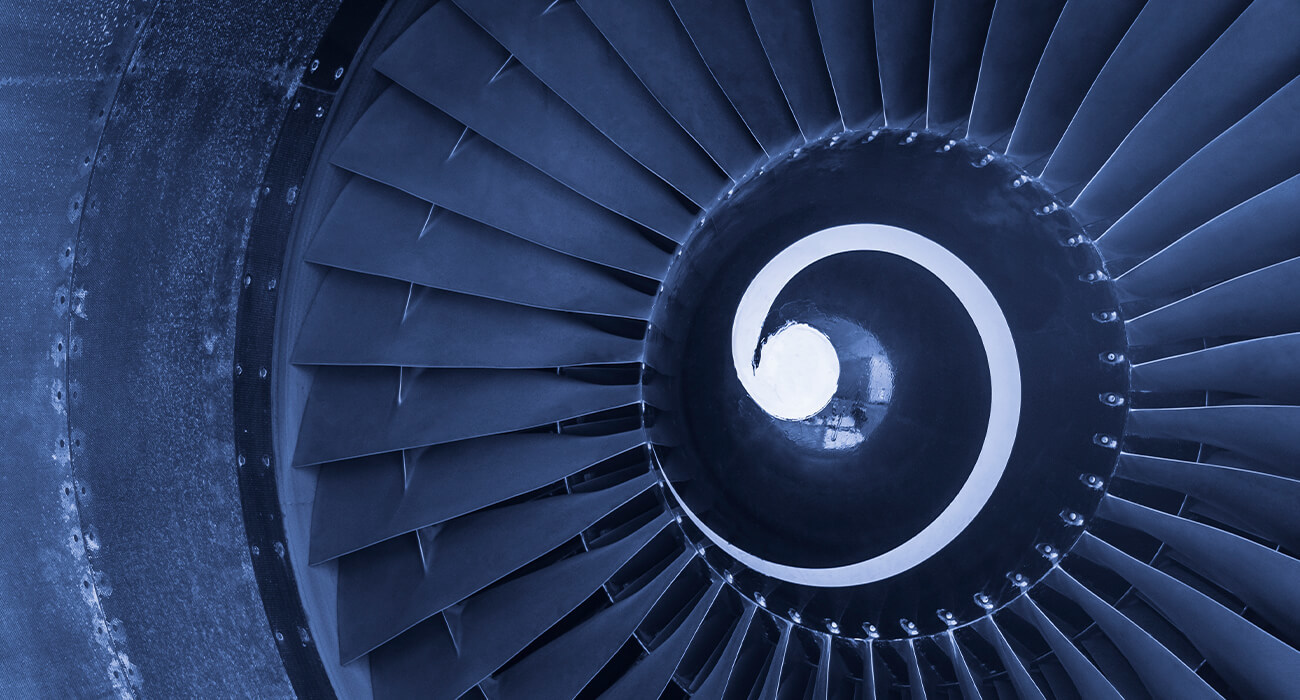
Unit layout
The ORC and other equipment are arranged in a two-story reinforced concrete structure. The evaporator, preheater, working medium pump, ORC turbine generator set and system valve are centrally arranged on one platform, and the condenser and liquid storage tank are arranged on the two-layer platform. The black water flash steam valve is arranged on the platform where the owner's low pressure flash pipe is located, and the valve is explosion-proof valve.
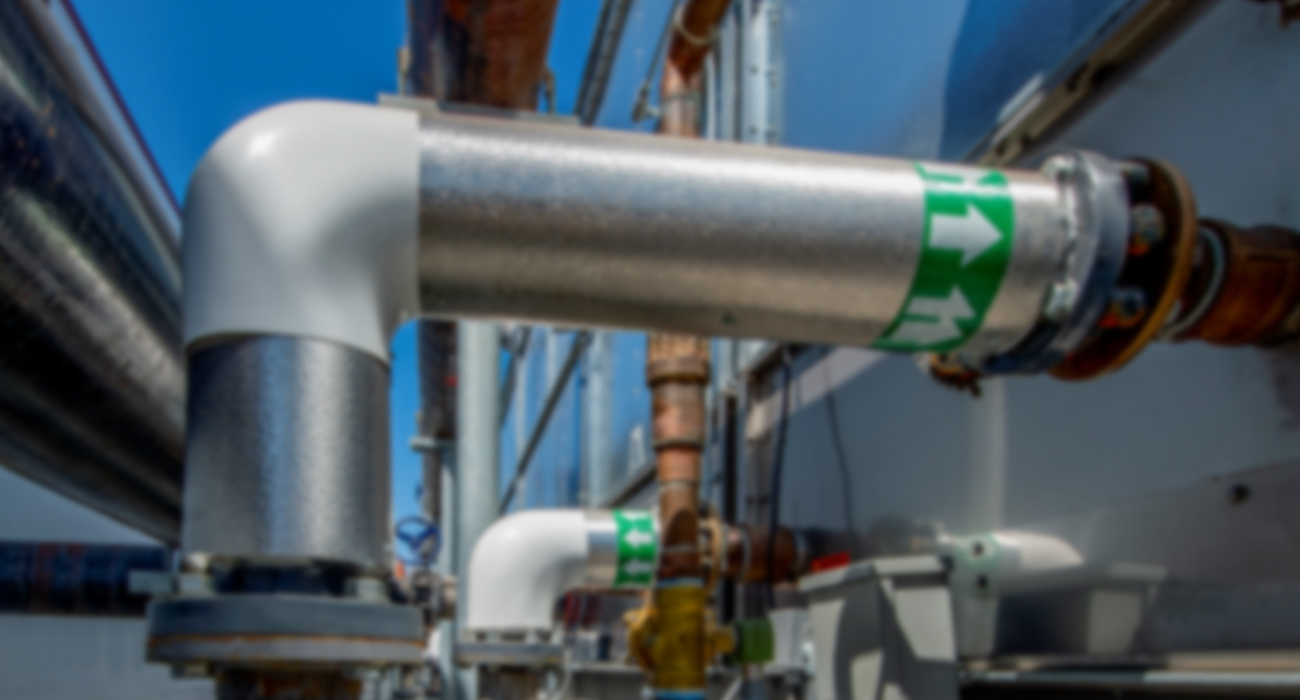
Cold source system
In this project, circulating cooling water is used to cool the organic working fluid. Similar projects can also choose evaporative condenser, water-cooled and air-cooled forms as cold sources according to the characteristics of the site.
Live Photo
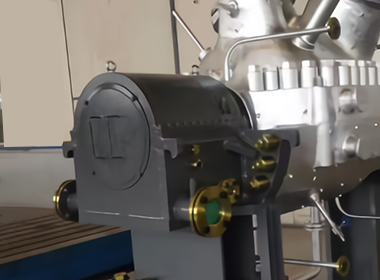
Project Photo
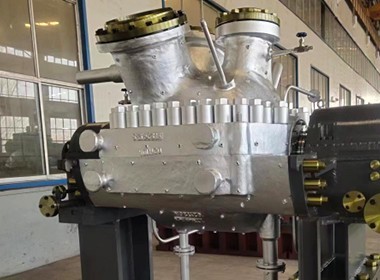
Project Photo
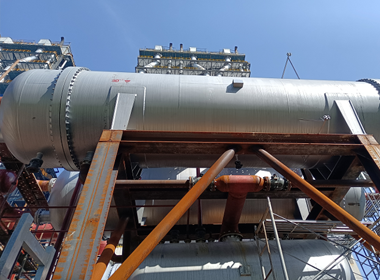
Project Photo

Official account


Xi 'an city:5th Floor, Building B, Jinpan (Tower),
Fengcheng 9th Road, Weiyang District, Xi'an City
Tel:+86 029-89190101
Ningbo city: No. 505 Dinghai Road, Zhaobaoshan Street, Zhenhai District
Tel: +86 18969840090
COOKIES
Our website uses cookies and similar technologies to personalize the advertising shown to you and to help you get the best experience on our website. For more information, see our Privacy & Cookie Policy
COOKIES
Our website uses cookies and similar technologies to personalize the advertising shown to you and to help you get the best experience on our website. For more information, see our Privacy & Cookie Policy
These cookies are necessary for basic functions such as payment. Standard cookies cannot be turned off and do not store any of your information.
These cookies collect information, such as how many people are using our site or which pages are popular, to help us improve the customer experience. Turning these cookies off will mean we can't collect information to improve your experience.
These cookies enable the website to provide enhanced functionality and personalization. They may be set by us or by third-party providers whose services we have added to our pages. If you do not allow these cookies, some or all of these services may not function properly.
These cookies help us understand what you are interested in so that we can show you relevant advertising on other websites. Turning these cookies off will mean we are unable to show you any personalized advertising.